Understanding Silicone Rubber Injection Molding Machines
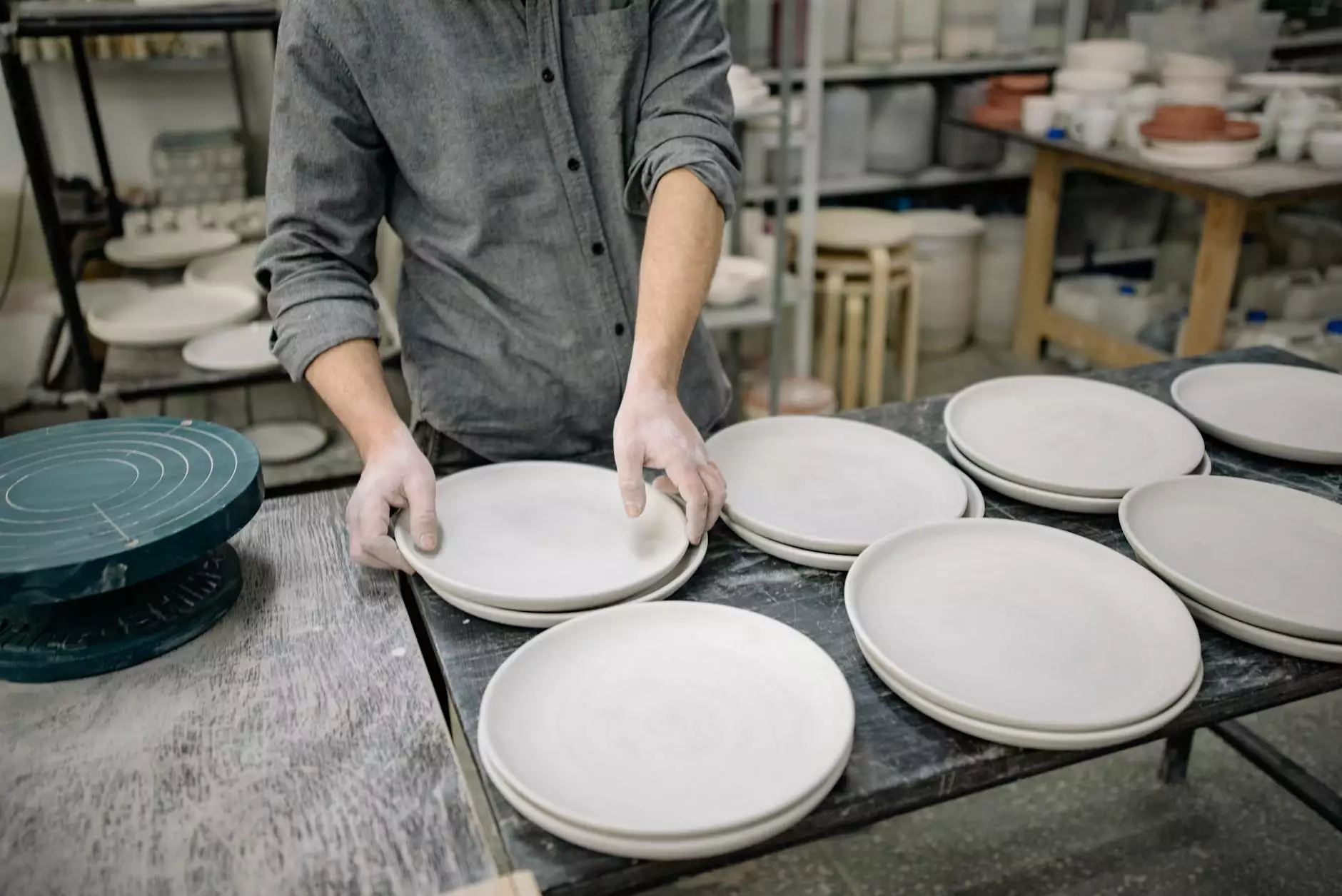
The world of manufacturing is constantly evolving, with silicone rubber injection molding machines playing a crucial role in producing high-quality components across diverse industries. This article delves deep into the functionality, advantages, and applications of these machines, focusing primarily on their significance in the electronics and medical supplies sectors.
What is a Silicone Rubber Injection Molding Machine?
A silicone rubber injection molding machine is an advanced piece of equipment that facilitates the production of silicone rubber products through an injection molding process. This process involves injecting liquid silicone rubber (LSR) into a heated mold, where it cures and takes shape. This machine is designed to ensure precision, consistency, and efficiency when creating intricate silicone components.
Key Features of Silicone Rubber Injection Molding Machines
Silicone rubber injection molding machines are equipped with several advanced features designed to enhance production efficiency and product quality. Some of these features include:
- Automated Control Systems: These machines often come with sophisticated control systems that allow precise monitoring of the molding process.
- Multi-Cavity Molds: The ability to use multi-cavity molds significantly increases production rates, making it possible to manufacture several parts in one cycle.
- Temperature Control: Effective temperature management is critical in the curing process of silicone rubber. Modern machines provide accurate temperature controls for optimal results.
- Eco-Friendly Operations: Many silicone rubber injection molding machines are designed to minimize waste and energy consumption, making them environmentally friendly alternatives.
The Importance of Silicone Rubber in Electronics and Medical Supplies
Silicone rubber is known for its superior properties, making it suitable for various applications, particularly in the electronics and medical supplies sectors. Here’s an overview of its significance in these industries:
1. Electronics
In the electronics industry, silicone rubber offers remarkable insulation and protection for sensitive components. It is resistant to moisture, heat, and various chemicals, ensuring that the electronic devices remain operational even in harsh environments. Some common applications include:
- Keypads and Switches: Silicone rubber is used in the production of tactile keypads due to its excellent feel and durability.
- Encapsulation and Potting: Silicone provides effective encapsulation for electronic circuits, protecting them from environmental damage.
- Sealing and Gaskets: Silicone rubber is widely used in seals and gaskets, providing reliable barriers against water and dust ingress.
2. Medical Supplies
The medical industry heavily relies on silicone rubber for manufacturing various essential products. Its biocompatibility, flexibility, and stability make it an ideal choice for medical applications, including:
- Catheters and Tubing: Silicone rubber is used for producing flexible medical tubing and catheters that are safe for long-term use in the body.
- Implants: Silicone is often utilized in surgical implants due to its compatibility with human tissue.
- Medical Devices: Many diagnostic and treatment devices incorporate silicone rubber components to ensure safe and reliable operation.
How Silicone Rubber Injection Molding Machines Operate
The operation of a silicone rubber injection molding machine follows several key stages:
- Preparation: The machine is set up with the appropriate mold and the liquid silicone rubber is prepared for injection.
- Injection: The liquid silicone rubber is heated and injected into the mold with precision, filling the cavities and ensuring no air pockets.
- Curing: Once the mold is filled, it is subjected to heat, allowing the silicone rubber to cure and take shape.
- Demolding: After the curing process, the mold is opened, and the finished silicone rubber parts are ejected.
- Quality Control: The final products undergo rigorous quality checks to ensure they meet predetermined specifications.
Advantages of Using Silicone Rubber Injection Molding Machines
Utilizing a silicone rubber injection molding machine offers numerous advantages that enhance manufacturing capabilities:
- High Precision: These machines provide exceptional accuracy, ensuring that every product meets strict tolerance levels.
- Efficient Production: The ability to use multi-cavity molds allows for increased production output without sacrificing quality.
- Cost-Effectiveness: Although the initial investment may be significant, the longevity and efficiency of silicone rubber products often lead to reduced long-term costs.
- Versatility: Silicone rubber can be colored and combined with various additives to produce a wide range of products suited for many applications.
The Future of Silicone Rubber Injection Molding Machines
The future of silicone rubber injection molding machines looks promising, with continuous advancements in technology paving the way for improved functionality and efficiency. Some key trends to watch include:
- Smart Manufacturing: Integration of Industry 4.0 technologies is likely to create smarter machines that can communicate data in real time, optimizing production processes.
- 3D Printing Integration: Combining traditional molding techniques with 3D printing could revolutionize product design and prototyping.
- Sustainability Practices: More manufacturers are focusing on eco-friendly practices, ensuring that machines use less energy and produce minimal waste.
Challenges Faced in Silicone Rubber Injection Molding
While there are many advantages to silicone rubber injection molding machines, some challenges need to be addressed, including:
- Equipment Costs: The initial investment in high-quality machines and molds can be high, though beneficial in the long term.
- Complexity of the Process: Mastering silicone rubber injection molding requires specific expertise and training.
- Material Limitations: While silicone rubber is highly versatile, certain designs may encounter limitations in moldability.
Conclusion
The silicone rubber injection molding machine stands as a vital asset in the manufacturing landscape, particularly within the electronics and medical supplies sectors. Its ability to produce high-quality, durable, and precise silicone rubber components makes it indispensable for businesses looking to innovate and expand their product range.
As technology continues to evolve, the relevance and functionality of these machines are likely to increase, offering even greater potential for productivity and sustainability. Embracing these industrial advancements will be crucial for businesses aiming to stay ahead in a competitive market.
For companies like Nolato, which specialize in producing sophisticated silicone rubber products, harnessing the power of these machines is essential. By investing in quality silicone rubber injection molding machines, they can ensure they meet the ever-growing demand for innovative products in the electronics and medical fields.