Understanding Concrete Batch Plant Cost: A Comprehensive Guide
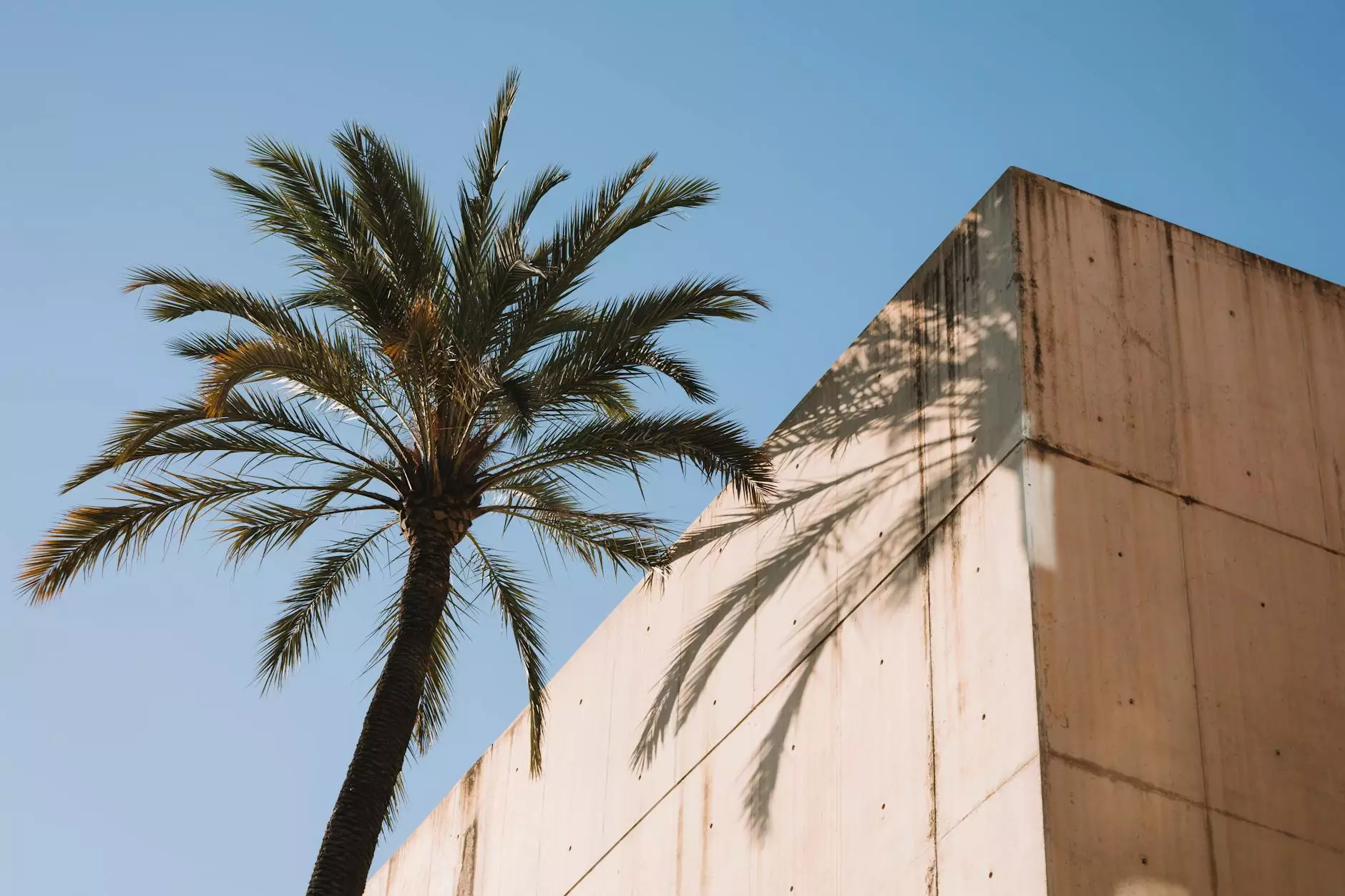
When delving into the construction industry, one of the most vital aspects that contractors and project managers need to understand is the concrete batch plant cost. This multifaceted factor can significantly influence a project’s overall budget and timeline. In this article, we will comprehensively explore what goes into the cost of a concrete batch plant, so that you can make informed decisions for your business.
What is a Concrete Batch Plant?
A concrete batch plant is a facility designed to combine various ingredients to form concrete. These facilities can range in size and complexity, from small, portable units to large, stationary plants that are equipped to handle high volumes of production. The key components of a concrete batch plant include:
- Cement Silos: Storage containers for cement, essential for maintaining an uninterrupted supply.
- Aggregate Bins: Hold various aggregates like sand, gravel, or crushed stone.
- Mixers: The heart of the plant where all ingredients are mixed to create concrete.
- Control Systems: Automated systems that monitor and control the batching process.
Factors Influencing Concrete Batch Plant Cost
Understanding the factors that influence the concrete batch plant cost is crucial for effective budgeting. Here are the primary components that can affect pricing:
1. Type of Concrete Batch Plant
There are various types of concrete batch plants, including:
- Stationary Plants: Typically used for large construction projects and have a higher initial investment.
- Mobile Plants: More flexible and typically less costly, but they may have limitations on output capacity.
- Ready-Mix Plants: Deliver pre-mixed concrete to construction sites, requiring specific infrastructure.
The type you choose will significantly impact the concrete batch plant cost.
2. Production Capacity
The production capacity of a concrete batch plant also plays a pivotal role in determining its cost. Larger plants that can produce higher volumes typically come with a higher price tag. Here’s a breakdown:
- Small Capacity: Suitable for small projects, generally more affordable.
- Medium Capacity: Offers a balance, catering to a broader range of projects.
- High Capacity: Designed for commercial and industrial projects, requiring significant investment.
3. Quality of Materials
The quality of materials used in constructing the batch plant, such as steel and electrical components, will affect the final cost. Investing in high-quality materials can lead to:
- Increased longevity of the plant.
- Reduced maintenance costs over time.
- Higher overall efficiency.
4. Location
The geographical location of your business can significantly influence the concrete batch plant cost. Considerations include:
- Transportation Costs: The distance to raw material suppliers can add to operational costs.
- Labor Costs: Regional variations in labor costs can affect initial and ongoing expenses.
Breaking Down Concrete Batch Plant Costs
To accurately assess the concrete batch plant cost, it is essential to break it down into various components. Here’s a detailed outline of potential costs:
1. Initial Capital Investment
This includes the purchase price of the plant, installation costs, and any needed site preparation. A detailed estimate might look like this:
- Purchase Price: $100,000 - $1,000,000 depending on the type and size.
- Installation Costs: $10,000 - $50,000 based on site conditions.
- Site Preparation: $5,000 - $20,000 for leveling and infrastructure.
2. Operational Costs
Ongoing costs are crucial to consider for a sustainable operation:
- Labor Costs: Typically range from $15 to $30 per hour depending on location and skill level.
- Maintenance Costs: Estimated at 10-15% of the plant’s value annually.
- Energy Costs: Vary based on local energy prices but are critical for ongoing operations.
3. Insurance and Permits
Operational insurance and necessary permits also contribute to the overall costs, which can include:
- General Liability Insurance: Costs typically range from $400 - $1,500 per year.
- Permits: Depending on local regulations, this can range from a few hundred to several thousand dollars.
Financing Your Concrete Batch Plant
Financing is a vital aspect of acquiring a concrete batch plant. Potential options include:
- Loans: Traditional bank loans or credit from equipment suppliers.
- Leasing: A less expensive initial option but may cost more in the long run.
- Grants and Incentives: Research local and federal programs that support construction businesses.
Conclusion: Making Your Investment Worthwhile
In conclusion, understanding the concrete batch plant cost is vital for any business operating in the construction industry. By evaluating the myriad of factors that influence costs—from the type and capacity of the plant to location and ongoing operational expenses—you can make well-informed decisions that will set your business up for success. Investing wisely in a concrete batch plant not only enhances your production capabilities but also positions you strategically against competitors in the market.
For more insights and expert advice on concrete batch plants and their costs, visit polygonmach.com, where you can find additional resources tailored to your machinery needs in the electronics and 3D printing industries.